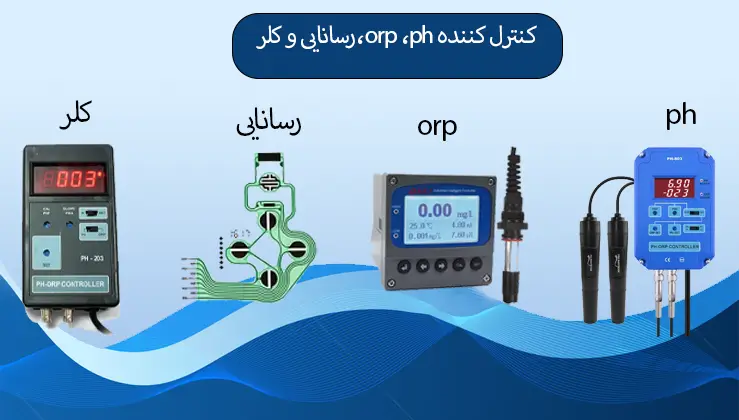
در این مجله پیامبر آب میخوایم در مورد کنترل کننده orp،ph، کلر و رسانایی چیست و چگونه کار می کنند؟ بپردازیم. مزایا و معایب، ویژگی و کاربرد های مختلف آن ها در صنایع مختلف را مورد بررسی قرار دهیم.
PH چیست؟
ph یک معیار لگاریتمی است که برای تعیین میزان اسیدیته یا قلیایی بودن محلول های مایع استفاده می شود.
در واقع پی اچ (PH) میزان غلظت یون هیدروژن را را در محلول تعیین می کند. با توجه به میزان غلظت این یون، اسیدی یا بازی بودن محلول مشخص می شود.
به طور کلی هر چه عدد پی اچ (PH) کوچک تر باشد، محلول اسیدی تر و هر چه مقدار پی اچ (PH) بزرگ تر باشد، محلول مایع بازی خواهد بود.
اسید چیست؟ اسیدها مواد شیمیایی هستند که یون هیدروژن (H+) دارند، و می توانند پروتون اهدا کنند. اسید ها خواص مختلفی دارند مانند: مزه ترش، توانایی تغییر رنگ برخی از مواد از جملا کاغذ تورنسل که آن را به رنگ قرمز در میاورد، واکنش با فلزات و باز ها.
باز چیست؟ ماده ای است که در آب حل شده و یون هیدروکسید (-OH) تولید می کند. محلول بازی خاصیت لغزنده دارد و در هنگام لمس آن می توان حالت لیزی را احساس کرد. باز ها کاغذ تورنسل را به رنگ آبی تغیرر می دهند، مقابل اسید ها هستند و می توانند آن هارا خنثی کنند.
دامنه PH چیست؟
برای تعیین دامنه PH یک بازه 0 تا 14 در نظر گرفته می شود. البته این تعیین بازه با میزان غلظت یون هیدروژن در ارتباط است.
اگر PH در دمای 25 درجه سلسیوس
- بیشتر از مقدار هفت، PH>7: اگر محلول ما بزرگ تر از عدد هفت باشد به معنی این است که محلول ما بازی است. یعنی غلظت یون هیدروکسید (-OH) از یون هیدروژن (+H) بیشتر است.
- برابر با عدد هفت، PH=7 : در این حالت محلول خنثی است، به این معنا که نه خاصیت بازی دارد و نه خاصیت اسیدی.
- کمتر از مقدار هفت، PH<7: در این صورت که محلول کوچک تر از عدد هفت باشد، محلول اسیدی است و غلظت یون های هیدروژن ( +H) از هیدروکسید (-H) بیشتر است.
اشکال مختلف مایعات دارای سطح نرمال مختلف pH هستند. به عنوان مثال، آب خالص با pH 7 خنثی است. خون کمی قلیایی با pH حدود 7.4 است. سطح pH ادرار با محدوده طبیعی بین 4.5 تا 8. بزاق دارای محدوده pH طبیعی بین 6.2 و 7.6 است.هر زمان که این مایعات خارج از محدوده طبیعی قرار گیرند، نشانه ای است که ممکن است دلیلی برای نگرانی وجود داشته باشد. هنگامی که سطح pH آب از محدوده طبیعی خود خارج می شود، این نشانه ای است که کیفیت آب به خطر افتاده است. وقتی سطح pH خون، ادرار یا بزاق از محدوده طبیعی خود خارج می شود، نشانه ای از وجود یک مشکل پزشکی است.
چگونه PH را اندازه گیری کنیم ؟
- کاغذ تورنسل (Litmus paper) : کاغذ تورنسل یک نوار کاغذی است که با یک رنگدانه طبیعی آغشته شده است. این رنگدانه در تماس با محلول اسیدی به رنگ های قرمز و با محلول بازی به آبی تغییر رنگ می دهد و روشی بسیار ساده است.
- نوار های ( PH strips ) : این نوار ها مشابه با کاغذ تونسل هستند اما با ترکیبات شیمیایی مختلفی آغشته شده اند تا طیف وسیع تری از دامنه PH را نشان دهند. این نوار ها دقت بیشتری نسبت به کاغذ تورنسل دارند.
- دستگاه PH meter : پی اچ متر یک دستگاه الکترونیکی است که با استفاده از یک الکترود مخصوص، محلول را اندازه گیری می کند. این دستگاه دقت بالایی دارد.
مزایای PH :
- این نتایج دقیقی را ارائه می دهد و مقدار pH دقیقی رانشان می دهد.
- برای انواع مختلف محلول ها استفاده می شود.
- محدوده اسیدی و قلیایی PH (pH 01 تا 14) را پوشش می دهد.
- یک مزیت اضافی PH این است که قابل حمل است.
- در مقایسه با خواندن نوار رنگ یا نشانگر pH، یک PH متر نتایج بسیار دقیقی ارائه می دهد.
معایب PH :
- PH متر اغلب برای کالیبراسیون مورد نیاز است.
- یک محلول بافر ویژه برای کالیبره کردن آن مورد نیاز است
- کالیبراسیون pH ممکن است تحت تأثیر دما و جذب دی اکسید کربن باشد.
- به دلیل شکننده بودن الکترودهای شیشه ای احتمال شکستگی وجود دارد.
ORP چیست و چگونه کار می کند؟
کنترل کننده orp،ph، کلر و رسانایی
ORP مخفف Oxidation-Reduction Potential یا پتانسیل اکسایش-کاهش است و به توانایی یک محلول برای گرفتن یا دادن الکترون اشاره دارد. به عبارت سادهتر، ORP نشان میدهد که یک محلول تا چه اندازه اکسید کننده یا احیا کننده است.
هنگامی که می خواهید آب را با اکسیدان هایی مانند ازن، برم یا کلر ضد عفونی کنید، ORP می تواند به عنوان روشی برای تعیین میزان موثر بودن گندزدایی استفاده شود. برنامه های مختلف به سطوح مختلف ORP نیاز دارند
ORP یک اندازه گیری پتانسیومتری است که در آن پتانسیل انتقال الکترون توسط یک الکترود فلزی بی اثر (پلاتین یا طلا) حس می شود و نسبت به الکترود مرجع داخلی – معمولا Ag/AgCl خوانده می شود. بازخوانی سنسور یک ولتاژ (نسبت به الکترود مرجع) با مقادیر مثبت ناشی از محیط اکسید کننده (توانایی پذیرش الکترون) و مقادیر منفی ناشی از یک محیط کاهنده (قابلیت دادن الکترون) است. حسگرهای ORP ساختاری مشابه سنسور pH دارند ، با این تفاوت که به جای یک لامپ شیشه ای (که مخصوص یون های هیدروژن به عنوان پایه اندازه گیری pH است) یک الکترود پلاتین (یا در برخی موارد طلا) دارد.
رابطه orp و ph
از آنجایی که pH یک اندازه گیری مستقیم و کمی برای یک گونه محلول (یون هیدروژن) است، سنسور pH در محدوده 2 نقطه ای، یعنی pH 7.0 (در اصل “شیب صفر”) و یک pH جایگزین مانند 4.0 یا 10.0 کالیبره می شود. حسگر pH نیاز به کالیبراسیون مجدد معمول دارد زیرا غلظت الکترولیت آن و کیفیت لامپ شیشه ای با گذشت زمان کاهش می یابد.
ORP یک اندازه گیری کمی نیست، بلکه صرفاً اندازه گیری ظرفیت مایع فرآیند برای پذیرش یا اهدای الکترون است. شما در واقع غلظت هیچ گونه محلول را اندازه گیری نمی کنید – هر قرائت میلی ولت به دست آمده صرفاً اندازه گیری های کیفی است. از این رو یک نقطه “کالیبراسیون” را می توان تنها با این فرض انجام داد که کنترل کننده ORP 0 mV را در 0 mV می خواند. پتانسیل میلی ولت اندازه گیری شده توسط کنترل کننده، اختلاف الکترود ORP و الکترود مرجع داخلی آن است که معمولاً دارای پتانسیل 200 میلی ولت در دمای اتاق است.
با تغییر pH، تعادل بین گونههای شیمیایی مختلف در محلول تغییر میکند. برخی از این گونهها خاصیت اکسید کنندگی یا احیا کنندگی قویتری دارند و در نتیجه بر ORP تأثیر میگذارند. hلکترودهای مورد استفاده برای اندازهگیری ORP اغلب تحت تأثیر pH قرار میگیرند. در تصفیه آب، هم pH و هم ORP پارامترهای مهمی هستند. افزایش ORP میتواند به ضدعفونی آب کمک کند، اما اگر pH بسیار پایین باشد، ممکن است به تجهیزات آسیب برساند.
کاربرد های ORP
ORP احتمالا رایج ترین روشی است که توسط کنترل کننده های شیمیایی برای اندازه گیری سطح ضدعفونی کننده و ارزان ترین نوع سیستم استفاده می شود.
پتانسیل کاهش اکسیداسیون: (ORP) خواص اکسید کننده هر ضدعفونی کننده موجود در آب را اندازه گیری می کند. هنگامی که کلر آزاد می شود تا اکسید شود، حسگرها یک میلی ولت را تولید می کنند که به عنوان ORP بیان می شود. اگر کلر آزاد و در دسترس نباشد، مقدار میلی ولت تولید نمی شود.
مهم است که به یاد داشته باشید که “P” در ORP مخفف پتانسیل است. ORP توانایی آب برای اکسید شدن را اندازه گیری می کند و بنابراین زمانی که ضدعفونی کننده اولیه کلر باشد به pH وابسته است. سطوح CYA میتواند بر خوانشهای گرفته شده توسط یک حسگر ORP تأثیر بگذارد، همانطور که سیستمهای نمک میتوانند. (اغلب در تاسیسات کلر نمک باید از فلزات خاصی برای الکترودها استفاده شود تا از رسوب روی سنسور جلوگیری شود و نصب و مراقبت صحیح از سنسورها اهمیت ویژه ای پیدا می کند.
صنایع شیمیایی: کنترل فرآیند های الکترو شیمیایی مانند آبکاری و تولید باتری
صنایع دارویی: در تولید دارو برای کنترل واکنش های اکسیداسیون-کاهش استفاده می شود.
مزایایORP:
نظارت در زمان واقعی: مانیتورهای ORP دادههای آنی را ارائه میدهند و پاسخ سریع به تغییرات در ماهیت اکسیداتیو یا کاهشدهنده یک محلول را ممکن میسازند. این پایش بلادرنگ به ویژه در فرآیندهایی که تنظیمات سریع لازم است بسیار مهم است.
کنترل فرآیند: صنایعی مانند تصفیه آب، آبزی پروری و تولید مواد شیمیایی از مانیتورهای ORP برای کنترل دقیق فرآیندهای خود بهره می برند. با حفظ سطوح بهینه ORP، این صنایع می توانند کیفیت محصول و کارایی فرآیند را تضمین کنند.
مقرون به صرفه: مانیتورهای ORP معمولاً در مقایسه با سایر سیستم های نظارتی مقرون به صرفه هستند. سادگی و قابلیت اطمینان آنها، آنها را به انتخابی جذاب برای کاربردهای مختلف، از جمله نگهداری استخر و تصفیه فاضلاب تبدیل کرده است.
تنوع برنامه ها: مانیتورهای ORP کاربردهایی را در زمینه های مختلف، از فرآیندهای صنعتی گرفته تا نظارت بر محیط زیست پیدا می کنند. آنها در تصفیه خانه های آب، استخرهای شنا، تولید غذا و نوشیدنی و حتی در آکواریوم ها برای حفظ کیفیت آب استفاده می شوند.
معایب ORP:
دقت محدود: در حالی که مانیتورهای ORP برای بسیاری از کاربردها موثر هستند، ممکن است دقت لازم برای فرآیندهای بسیار حساس را نداشته باشند. در موارد خاص، اندازه گیری ها و حسگرهای اضافی ممکن است برای نظارت جامع لازم باشد.
تعمیر و نگهداری الکترود: الکترودهای مانیتورهای ORP می توانند در طول زمان تخریب شوند و بر دقت اندازه گیری ها تأثیر بگذارند. نگهداری منظم، کالیبراسیون و تعویض گاه به گاه الکترودها برای اطمینان از عملکرد قابل اعتماد ضروری است.
تداخل و آلودگی: قرائت ORP می تواند تحت تأثیر تداخل سایر مواد شیمیایی یا آلاینده ها در محلول قرار گیرد. درک شرایط خاص و تداخل احتمالی برای نظارت دقیق بسیار مهم است.
کلر چیست و چگونه کار می کند؟
کلر روشی برای تصفیه انواع آب استخر خصوصی و عمومی استفاده می شود.
کلر را به عنوان یک گاز سمی زرد رنگ مایل به سبز میشناسند که در صنایع مختلف به عنوان یک ماده تکمیلی نقش مهمی دارد. این گاز که دو برابر از هوا سنگینتر است، با بوی بد میتواند به عنوان یک ضد عفونی کننده، تاثیر بسیاری داشته باشد. علامت اختصاری گاز کلر Cl است که به دلیل قرارگیری در دسته بندی هالوژنها، خاصیت الکترونگاتیوی قوی دارد.
این ماده در دو نوع گاز و مایع برای تولید سایر محصولات استفاده میشود. با توجه به اینکه کاربرد کلر طیف وسیعی از صنایع و تولیدات را در بر میگیرد، در انواع مختلف هیپوکلریت سدیم (کلر مایع)، هیپوکلریت کلسیم ( کلر پودری )، دی اکسید کلر (کلر ژلی) گاز کلر، تری کلرو ایزو سیانوریک اسید سدیم و هیپوکلریت لیتیم تولید میشود که هر یک برای مصارف مشخصی کاربرد دارند.
کلر نیز دارای عوارض جانبی است که می تواند برای انسان آزار دهنده باشد و یا حتی خطرناک باشد. کلر بوی بسیار مشخصی دارد که اکثر آنها ناخوشایند به نظر می رسند و برخی آن را پرمخاطره می دانند. “فاکتور خارش” نیز وجود دارد. کلر می تواند باعث شود که پوست خاصی خارش و تحریک شود. یون هیپوکلریت باعث می شود بسیاری از پارچه ها وقتی که بلافاصله پس از خروج از استخر شسته نمی شوند ، سریع محو شوند. به همین دلیل است که لباس شنا شما در اوایل تابستان محو و فرسوده به نظر می رسد.
ترکیبات اصلی کلر
- هیپوکلریت سدیم (Sodium Hypochlorite) : یکی از رایج ترین ترکیبات کلر است که به صورت محلول آبی(وایتکس) یافت می شود. یک ضد عفونی کننده قوی در صنایع تصفیه آب، غذایی، پشکی و خانگی به حساب می آید.
- هیپوکلریت کلسیم (Calcium Hypochlorite) : به صورت پودر یا قرص موجود است به عنوان ضد عفونی کننده قوی در تصفیه آب استخر ها و تصفیه آب آشامیدنی استفاده می شود.
- پلی ونیل کلراید (PVC) : یک پلاستیک سخت و مقاوم است از پلیمریزاسیون ونینیل کلرید تولید می شوددر ساخت لوله ها، کابل ها، پنجیره ها و بسیاری از محصولات دیگر استفاده می شود.
- دیاکسید کلر (Chlorine Dioxide) : گازی زرد مایل به سبز با خاصیت ضد عفونی کنندگی قوی است برای گند زادایی آب آشامیدنی، صنایع غذایی و کاغذسازی استفاده می شود. به دلیل قدرت بالای اکسید کنندگی، در خذف بو و رنگ مواد آلی موثر است.
- ترکیبات گازی: اینها ترکیباتی هستند که شامل واکنش گاز (C12) با سایر مواد است. اسید هیبوکلر زمانی تشکیل می شود که گاز (HOCL) زمانی تشکیل می شود که در آب با CL حل می شود و با آن واکنش می دهد.
- کلرید سدیم (Sodium Chloride) :کلرید ها ترکیباتی هستند که هنگام ترکیب اتم ها ی CL با فلزات یا عناصر دیگر به وجود می آیند. مانند: نمک خوراکی (NaCL)، کلرید کلسیم(CaCL2) و کلرید پتاسیم (KCL).
کاربرد های کلر:
کلر مواد شیمیایی است که در صنایع مختلف به طور مستقیم و غیرمستقیم توانسته کاربردهای گستردهای داشته باشد.
- تصفیه آب و فاضلاب: کلر یکی از قوی ترین و پر کاربرد ترین مواد ضدعفونی کننده آب است. با از بین بردن باکتری ها، ویروس ها و سایر میکروارگانیسم های بیمازی زا، آب را برای آشامیدن و مصارف صنعتی ایمن می کند. برای از بین بردن عوامل بیماری زا، کاهش بار آلی، در تصفیه آب استخر ها و جلوگیری از رشد جلبک استفاده می شود.
- صنعت شیمی: کلر در تولید طیف وسیعی از مواد شیمیایی از جملع پلاستیک های (PVC)، حلال ها، رنگ ها، داروها و آفت کش ها استفاده می شود. در صنایع نساجی، کاغذ سازی و تولید مواد شوینده به عنوان سفید کننده استفاده می شود.
- تصفیه آب استخر: کلر یکی از مهم ترین مواد شیمیایی مورد استفاده در تصفیه آب استخر است. این ماده به دلیل خاصیت ضدعفونی کنندگی قوی، نقش بسیار مهمی در خفظ بهداشت وسلامت آب استخر ایفا می کند. کلر با از بین بردن باکتری ها، جلبک ها و سایر میکرو ارگانیسم های بیماری زا، از بروز بیماری های پوستی، چشمی و عفونت های دستگاه گوارش جلوگیری می کند. کلر با جلاو گیری از رشد جلبک ها، آب استخر را شفاف و تمیز نگه می دارد. کلر با اکسید کردن مواد آلی موجود در آب از رشد باکتری ها و ایجاد بوی نامطبوع جلوگیری می کند.
- صنایع کاغذ و خمیر کاغذ: کلر برای سفید کردن خمیر کاغذ و از بین بردن رنگدانه های طبیعی آن استفاده می شود.
- درصنایع نساجی، کلر برای سفید کردن پارچه ها ئ از بین بردن لکه ها به کار می رود.
مزایای کلر:
- ارزان بودن
- باقی ماندن کلر در آب: پس از ضدعفونی کردن با کلر، مقداری کلر در آب باقی می ماند و در صورت ورود مجدد آلودگی به آب ، کلر باقیمانده باعث ضد عفونی شدن آن می شود.
- مؤثر بودن در برابر میکروارگانیسم های بیماری زا
- مؤثر بودن در اکسیداسیون ترکیبات آلی و غیرآلی خاصقابل انعطاف بودن میزان تزریق کلر
معایب کلر :
- کلر در تماس با ترکیبات آلی موجود درآب واکنش نشان میدهد و محصولات جانبی مانند تریهالومتانها THMs و هالواستیک اسید HAA5 تولید میشوند. این مواد سمی و جهشزا میباشند. ذکر این نکته مهم است که که با حذف مواد آلی قبل
- از ضدعفونی با کلر میتوان تولید این محصولات را به حداقل رساند.
- ایجاد مزه و بو میکند.
- کلر نمیتوانند بعضی از میکروارگانیسمها مانند پروتوزا کیستدار را از بین ببرد.
- باقیمانده کلر حتی در غلظت های بسیار پایین برای حیات حیوانات آبزی سمی است.
- تمامی اشکال کلر سمی هستند، بنابراین ذخیره سازی، حمل و نقل و نگهداری آن خطرناک است و نیازمند مقررات ایمنی میباشد.
سنسور رسانایی چیست و چگونه کار می کند؟
سنسور رسانایی ابزاری جهت سنجش است که برای تعیین رسانایی الکتریکی محلول استفاده می شود. رسانایی الکتریکی آب به معنای توانایی آب برای هدایت جریان است. یکی از معیارهای مهم در تعیین کیفیت آب است.رسانایی سنج ها دستگاه هایی هستند که برای اندازه گیری رسانایی الکتریکی یک مایع استفاده می شوند. آنها به طور گسترده در بخش های علمی، صنعتی و کشاورزی برای نظارت و کنترل کیفیت سیالاتی مانند آب، روغن و سوخت استفاده می شوند. این مقاله اصول عملکرد سنج های رسانایی، نحوه کار و کاربرد آنها را توضیح می دهد.
سنسور رسانایی در صنایع متفاوتی از جمله تصفیه آب، داروسازی و صنایع غذایی کاربرد گسترده ای دارند. یکی از دلایل اصلی استفاده از سنسور هدایت الکتریکی، قابلیت تبدیل تغییرات فیزیکی و شیمیایی به سیگنال های الکتریکی می باشد که در بسیاری از زمینه ها بسیار مفید هستند. سنسور اندازه گیری هدایت الکتریکی جهت سنجش رسانایی الکتریکی در مایعات اسیدی، خورنده، قلیایی، دوغابها و مایعات دارای املاح نمکی مورد استفاده قرار می گیرند.
مزایای رسانایی :
- کنترل روی ph,orp,کلر
- در مصرف مواد شیمایی صرفه جویی می شود.
- به صورت خودکار و خود به خود این کار صورت می گیردو به صورت دستی نمی باشد.
معایب رسانایی:
- هزینه بالاتر
- نیاز به تعمیر و نگهداری دارد.
آخرین نظرات